Our Environmental Claims Services deliver on our underwriting promise by providing unparalleled claims service to our insured’s.
Unlike most MGA’s, our team handles claims in house through a dedicated and integrated specialist claims team that has delegated claims authority. Our claims professionals are experienced specialists, not generalists, and only service the policies we write. There is one point of contact and direct access to the Head of claims is a phone call or email away.
This service extends beyond handling claims and we stand ready to assist our insureds from underwriting through resolution of the claim. We have nationwide access to counsel, consultants and experts ready to respond to our insured’s needs.
We also offer value added services including:
- 24/7 Emergency Response Services with environmental consultants and engineers at theready to provide assistance in the event of an environmental emergency (800- 347-4384 (press 1) / ERS@enviant.com
- 24/7 Crisis Management with nationwide crisis response with up to $250,000 in complimentary crisis management expense
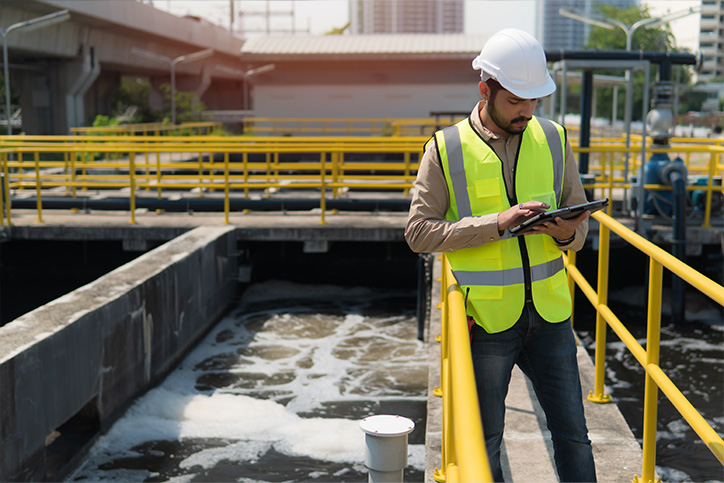
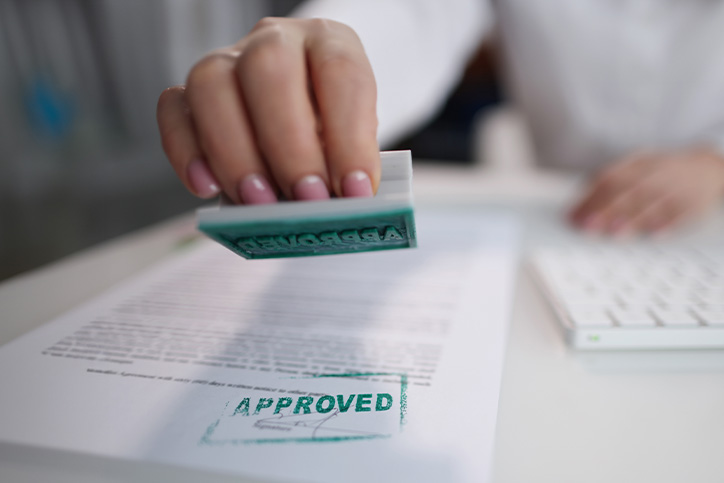
Submit a claim:
environmental.claims@enviant.com
EMERGENCY RESPONSE SERVICE HOTLINE
1-800-347-4384
ERS@enviant.com
Thank you for placing your trust in One80 Intermediaries. Our environmental insurance and risk management claims team is here to help.
Let us know how we can be of service to you. For any additional inquiries please contact:
Sean Upton – Senior Vice President, Head of Environmental Claims
Enviant, a division of One80 Intermediaries
supton@enviant.com
Direct: 646-946-0021
Pollution Legal Liability Claim Scenarios
Environmental insurance policies have become an accepted solution for many businesses to manage their pollution exposure. Whether the coverage is provided through a monoline site pollution policy or through the site coverage under a combined form, no matter how carefully insured plan, gradual or sudden and accidental pollution events happen. Often times the pollution event itself is not the main driver of damages and costs, but the response and inadequate remediation response that can greatly exacerbate the situation.
Here are few claims examples that provide some insight into what can happen:
Chemical Blending Company
The insured is a regional chemical blending and chemical manufacturing company. After small volume testing a new chemical blend “recipe” the insured commences bulk blend production. During the blending operation the chemical blend begins to overheat and combust releasing flammable gases (A calculation error underestimated the exponential heat increase with chemical blend volume increase). Effort to cool the blending vessel were unsuccessful and the insured attempted to move the vessel with an overhead crane to a different area in the facility to isolate the vessel, permit controlled venting, scrubbing the releases gases, and away from stored flammable products. During the lift a short in the overhead electric crane ignited the released gases causing a flash fire that soon engulfed the entire warehouse. The local fire department responded pouring millions of gallons of water on the fire. The warehouse contained thousands gallons of completed products including polymers (that floats on water). The water runoff ran into an adjacent storm water culvert that drained to a stream and two ponds of an adjacent landowner, as well as the significant portion of the insured’s property. Upon notification the carrier mobilized emergency response contractors who began containing the fire water runoff and conducted air monitoring (a local community college was located downwind of the insured facility). Air monitoring revealed no human health concerns and the fire was controlled to burn itself out.
Once extinguished the contractors began remediating the ground on the site to eliminate and contain any further source for run-off and began cleaning the streams and ponds. It was then discovered that a backbone fiber optic cable for the entire state was located in an adjacent right of way that contained contaminated soil. The soil was contaminated by the fire water runoff that contained polymers and other chemicals. Due to the sensitivity of the fiber optic cable a 700’ section of the right of way was excavated by hand. With drought breaking rain storms approaching the contractors built berms around the insured facility, diverted run-off to newly constructed lined retention pond, and set up a battery of frac tanks to handle contaminated water processing and disposal. The proactive measures mitigated further offsite contamination and contained the contamination on site. This enabled an orderly demolition and debris removal operation, followed by a complete site remediation without further off site contamination. Thousands of tons of contaminated soil was excavated and disposed of, and the stream and ponds were excavated and restored. The clean-up costs were several million dollars, but proactive action mitigated the extent of the damages significantly and was viewed favorably by the local regulators which assisted with permitting during the rebuild.
Animal Feed Company
The insured manufactures animal feed using recycled vegetable oil. During maintenance work an employee ignited insulation which in turn ignited dust in the prilling tower causing a flash fire that soon engulfs the entire facility, including the thousands of gallons of vegetable oil stored on site. The local fire department responded and began pouring water onto the building. The carrier was notified immediately and its emergency response and crisis response team was activated. Air monitoring confirmed that the smoke plume was benign and the previously ordered shelter in place was lifted. The insured CEO with guidance from the crisis management teams went on local television together with the Fire Chief to explain what had occurred and that there was no health concern. The emergency response team discussed options with the Fire Chief who backeddown the fire water to a control situation as runoff into storm water drains could impact nearby rivers. The storm water drains were capped off and the contaminated water was pumped and disposed of.
After 2 days the fire was extinguished with foam and contained to the basement area of the facility where the oil was stored. The local POTW refuses to permit the contaminated fire water to be discharged to the sewer system so an onsite processing system put together using the insureds onsite waste water treatment plant. The water was processed on site and transported to another POTW that had the capacity to handle the volume. As the contaminated water was contained to the basement processing and disposal could be done over time without the potential for further contamination, as well as permitting the insured to commence demolition and debris removal on other buildings. The remediation was completed in a month.
Plastic Crate Manufacturer
The insured is a national plastic crate manufacture. Employees were tasked with cleaning excess plastic off crates in the outside storage area using propane torches. During a lunch break a rag ignited on a hot crate that work had just been completed on. This eventually ignited surrounding crates and shortly thereafter the entire plastic crate stack of thousands of crates began burning creating a massive black smoke plume that travelled several miles over highways and over an adjacent residential neighborhood depositing particulate matter. One of the largest soda bottling company located adjacent to the insured’s facility was forced to shut down operations to avoid contamination during the highly automated and sterilized bottling process. Significant fire water contaminated with burned plastic released offsite to several storm water drains. Claims were made for bodily injury and property damage to adjacent home owners and motorists traveling on the nearby highway. The local air regulators threatened fines, the storm water system had to be flushed and decontaminated, soil at the insured’s facility had to be remediated and the bottling company brought claims for business interruption and cleaning costs to their air scrubber system.
Metal Recycler
The insured is a large metal recycler with numerous scrap metal recycling yards. An employee while loading metal from a pile onto a conveyor with a grapple punctures a drum containing a minimal quantity of a hazardous chemical. (The drum has previously been dropped off by a one- man metal recycler and was hidden under other scrap metal during unloading). The chemical leaked and came into contact with the air and moisture from rain creating a toxic plume that spread over the yard and across the street to neighboring businesses requiring mandatory evacuations. Claims are brought by the adjacent business for business interruption, employees of the adjacent businesses and invitees at the insured location for inhalation injuries and property damage claims for damage to vehicles. The regulators issued a directive for a clean-up of the area contaminated by the liquid. During the excavation of the soil additional other contamination was found resulting in a larger site investigation and subsequent remediation.
Dry Cleaner
The insured is a family dry cleaning business that leased a suite in an industrial complex from the property owner. The insured’s lease ended and the insured vacated the premises. The property owner then performed indoor sample and discovered high levels of PCE. Further investigation reveals high levels of contamination in the underground water below the premises leased by the insured. The property owner is directed to clean-up and install a vapor mitigation system. The owner demands reimbursement from the insured alleging that the insured’s solvents used in the insureds dry cleaning operation and improper handling of PCE caused the contamination. The insured vigorously denies that it caused the contamination and provides complete and detailed purchase and disposal records for all solvents used at the facility. The insured was no longer in business, and did not have finances to mount a defense, but had significant attachable personal assets. An investigation by the local regulator to delineate the contaminated water plume revealed anomalies. The carrier retained appropriate experts and entered into discussions with the regulators.
Upon further investigation and analysis, it was determined that large amounts of PCE were disposed in the planter box near the backdoor of an adjacent and now defunct printing operation that used extensive amounts of chemicals in its operations but failed to properly register with the local regulatory authority. It was determined that based upon an isotope analysis that the contamination under the premises leased by the insured was caused by the PCE disposed in the planter box that then migrating through the soil to the high water table and then flowed down gradient with the water under the premises where the dry cleaning operation was located and then released up into the premises operated by the insured.
Fertilizer Distributor
The insured is a large fertilizer distributor. Employees performing welding work on metal storage bin walls cause a bin of fertilizer to begin to smolder. Employee attempts to douse the fire were unsuccessful and a full fire commenced spreading through the storage warehouse. The facility also stored ammonium nitrate. The local fire department responded and upon learning of the ammonium nitrate stored on site immediately withdrew all firefighting personnel and equipment, creates a 2-mile radius perimeter and ordered the evacuation of the town. Close to 50,000 people evacuated and numerous large processing plants were forced to shut down. The evacuation orderwas lifted 8 hours later. Thousands of inconvenience, bodily injury and property damage claims were brought alleging exposure to toxic fumes and particulate matter from the burning fertilizer. The fire burned out and there was no direct fire damage beyond the perimeter of the insured’s warehouse. The soil over the entire site had to be remediated prior to reconstruction of the warehouse.
High Rise Apartment Owner
The insured owned a portfolio of over 50 high rise apartment buildings in a metropolitan area. The apartment building have large cooling towers for the central air for the building. During the summer a legionella outbreak in the neighborhood resulted in sickness and deaths to several elderly residents in a nearby retirement high rise. Local officials begin testing water of all buildings in the area and demand remedial action. Environmental experts are retained and testing results reveal legionella in the insured’s water system. The insured requests sampling of the strain of legionella in the sick and diseased and it is determined that the strain the cause the sickness and death did not emanate for the insured’s water tower. Other buildings did not perform sufficient or sophisticated testing and could not provide definitive evidence of the strain of legionella in their systems resulting in continued regulatory scrutiny.
Low Rise Apartment Owner
The insured owned a large portfolio of 4 to 6 story apartment buildings in a large city. During an annual doctors visit an infant of a tenant in the building tested for elevated blood lead levels (BLL) requiring chelation and other treatment. As required the local health department is notified and inspects the apartment and finds lead based paint in various rooms of the apartment that are above the threshold level. The parent immediately retain counsel and threaten litigation behalf of the child alleging cognitive impairment and multiple millions in potential lost earnings. The carrier retained counsel and completed its own testing and sampling of paint chips in the apartment. Based upon the testing results and the fact that the paint was intact in the apartment the local authorities testing was challenged. The challenge was ultimately upheld and the notice to abate was rescinded by the local authority after it was discovered that the testing device was improperly calibrated and was providing false positive results. The local health department continued its investigation and discovered an alternate source of lead paint exposure in the baby sitters’ apartment.
Bourbon Distillery
The insured is a large Bourbon Distillery. Plaintiffs filed a class action suit seeking property damage caused by “whiskey fungus”. It was alleged that during the bourbon aging process roughly 2 percent of the ethanol escapes through the wood of the barrels. (“the angels’ share”). Whiskey fungus has also been known for centuries, and has been identified as Baudoinia compniacensis. While not known to be hazardous to human health it creates a gummy, sooty film on walls and vehicles. It can be scrubbed off with bleach or power washed, but it is tenacious. The plaintiffs alleged that they had to expend an abnormal amount of time and money cleaning surfaces in and around their property, including gutters, siding, fencing and cars; and that whiskey fungus and the extreme cleaning methods necessary for its removal cause early weathering of surfaces affected by the fungus. The distillery argued that allegedly tortious conduct, the emission of ethanol from whiskey aging or other facilities, falls directly within the class of activities regulated by the Clean Air Act, and that ethanol emissions are explicitly authorized by state operating permits issued under the CAA.
School District
The insured is one of the largest school districts in the country. A group of teachers and students at a high school in the district alleged illnesses ranging from unexplained hair loss and skin rashes, to thyroid cancer and persistent migraines. The claimants alleged that their illness was directly related to a construction project which removed 1,000 cubic yards of PCB contaminated soil from the school grounds. The school was built on donated land that had historically housed a manufacturing facility that used PCB in the products. Construction was also done on several classrooms allegedly contaminated with mold. The high school attracted media attention and was pressed to conduct further environmental tests and medical studies and monitoring. The school enrolls more than 1,100 middle and high school students.
Golf Course
The insured owns and operates several very exclusive golf courses. Heavy rain occurred after the application of pesticide and herbicides to the golf course, washing the pesticide into an onsite pond. Pesticide laden run off impacted protected species and wetlands. State EPA ordered investigation and restoration of wetlands, and assessed natural resource damages to endangered species and wetlands. Significant clean-up costs were incurred as much of the impacted area was difficult and sensitive to access with heavy equipment requiring manual remediation
Oil Pipeline Operator
The insured is a large regional oil pipeline owner/operator. A dime sized hole occurred in a very remote area of the a 6” mainline and was not discovered for several days. Approximately 400 barrels of crude oil was released. When the landowner discovered the leak the insured responded immediately and began repair and remediation operations. Within days of the remediation commencing the area was inundated with heavy rain and below freezing temperatures which was unprecedented for this region. This resulted in residue crude oil washing down stream into a small indigenous forest area. Due to the rain the area became inaccessible and a timber mats had to be trucked in to construct 2-mile access road to permit equipment access to the affected area. The rental and placement of the mats alone cost in excess of $1M. A creek in the forest had to be manually cleaned for over a month and various dykes and dams had to be constructed to catch contaminated rain water to prevent further distribution of the residual crude oil that was not initially clean up. The clean-up project that prior to the inclement weather only impacted several hundred square feet took 90 days to complete and required the mobilization of significant equipment and personnel.
Airplane Part Manufacturer
The insured is a large internationally known aircraft specialty metal parts manufacturer. The insured stored dust containing heavy metals in an uncovered dumpster behind the facility. During a sudden and unexpected heavy thunderstorm, the storm water mixed with the dusts, forming a slurry which leaked out of the dumpster and ran off-site. Soil testing of a nearby stream bank revealed high levels of lead, cadmium, and mercury. The local environmental regulators directed the insured to remediate the contamination.
Fish Canning Facility
The insured owned a fish canning facility in a remote area of a large state. While excavating an area to expand the production line soil contaminated with heating oil and diesel was found a shallow depth and in the water table (The facility was located on a river). Further investigation uncovered various undocumented pipes that were previously connected to above ground storage tanks that had long since been removed by the previous owner decades ago. The pipes were not properly drained when disconnected and overtime corroded and released the hydrocarbons. The insured had to excavate the pipes (some that ran under existing) and remove and remediate significant amounts of contaminated soil. Due to the remote area and very short window to conduct these operations the clean-up costs were extensive.
Ski Resort
The insured owns and operates a portfolio of ski reports across the united states. During the summer months an above ground tank used for storing diesel fuel for water pumps for snow blowing operations developed a small and slowly leaked several hundred gallons of diesel fuel over the course of several weeks. The diesel fuel migrated to a nearby water pond used to supply water for snowmaking. It was only after a hiker noticed a sheen on the water in the fall that the insured discovered the release. The local regulators required the pond to be completely remediated before any water could be used for the coming ski season that was critical for the insured’s financial wellbeing. After initial remediation of the soil and skimming of the water an onsite pump and treat system was set up to process the contaminated water, so that the pond could be used for the new ski season.
Gas Station Servicing Company
The insured is a national gas station equipment maintenance and servicing company that, among other things, removes and installs USTs and associated piping and leak detection equipment, along with installing, maintaining, and repairing fuel dispensers. The insured is called in to correct a pressure issue on the piing system between the USTs and fuel dispensers. The insured technician diagnoses an issue with the Veeder-Root leak detection system and replaces a valve. A few weeks later, the customer calls and advises that it has a fuel shortfall. The insured investigates and finds no leaks or issues and cannot identify any problems. After continued shortages, the customer sends in its own team to investigate and the team advises the insured that a coupling nut on the Veeder-Root leak detection system was loose, and that several thousand gallons of gasoline had leaked into the sump and adjacent soil and ground water.
The local regulators direct that clean-up commence immediately and that a pump and treat system be installed. The customer alleges that the leak was caused by the technician failing to properly tighten the valve coupling, and that the insured is responsible for all the remediation costs. The customer is uncooperative in providing documentation, including any objective evidence to show that the valve coupling was the cause of the release. The customer files a suit seeking reimbursement of all remediation costs. The carrier responds and investigates, by obtaining complete records, including historical records and retaining experts to determine the origin and cause. The investigation reveals pre-existing contamination of the site and an antiquated and poorly managed fuel storage and dispensing system. The valve and coupling were removed and discarded prior to notification to the insured. After mounting a vigorous defense, the matter is resolved for a nominal amount.
Energy Efficiency Contractor
The insured is a well-known regional energy efficiency contractor that provides energy audits and corrective measure contracting. During an energy efficiency upgrade and home expansion project, a new high efficiency oil furnace is installed by a subcontractor to handle the expanded heating demands. The homeowner is advised that the existing AST is in poor condition and that the entire storage and piping system should be checked. The homeowner requests the installation of a new above-ground storage tank only, and the subcontractor completes the installation and connection to the existing supply line. Unbeknownst to the heating subcontractor, the supply line is still connected to an old underground home heating oil tank. After several months, the homeowner reports excessive home heating oil consumption and the newly installed furnace and AST are checked and re-checked. No problems or issues are found, and the home heating oil supplier keeps delivering and filling the AST.
A few months later, a local EPA inspector notices an oil sheen in a gully next to the roadway and investigates. It is discovered that the oil from the AST was not only supplying the furnace but also a leaking UST. The home was purchased out of foreclosure and the prior owner had not used the UST in years. The years of disuse had caused condensation and, ultimately, failure to the UST. The subcontractor only carried CGL coverage and did not have contractors pollution coverage. The clean-up cost in excess of $300,000 and the homeowners’ carrier subrogated against the insured, its subcontractor, and the oil supply company. Litigation dragged on for several years with hundreds of thousands spent in legal defense costs. After a thorough investigation and a vigorous defense, the claimant discontinued the litigation.
General Contractor
The insured is a large reputable commercial construction contractor. During the expansion of an air traffic control tower at a large regional airport, insured employees used a propane powered generator to power equipment in the newly constructed area. The employees set up the generator venting to the outside of the building but did not realize that the generator exhaust was directly opposite an air intake for and HVAC system, resulting in fumes being circulated throughout the control tower, causing bodily injury to several air traffic controllers and resulting in a temporary shutdown of the airport. The air traffic controllers were employed by a subcontractor to the airport operator. The air traffic controllers sued the airport operator and the contractor. The insured contractor was obligated by contract to defend and indemnify the airport operator. The air traffic controllers alleged long-term neurological deficits that precluded them from returning to work as air traffic controllers.
HVAC Contractor
The insured is a large regional HVAC contractor that contracted with a chain of movie theatres to install the air conditioning systems. The movie theatre provided the architectural and engineering specifications. Sometime after the completion of the project and after the theaters opened for business, the movie theatre company complained of mold and mildew in several theatres and improper humidity levels and sought emergency remediation and business interruption costs during the down time. Upon investigation if was determined that a humidistat had been incorrectly wired, causing improper balancing and improper humidity control within the theatres. The insured’s records indicated a correct installation and testing prior to the project completion. The movie theatre filed suit. During discovery it was determined that the movie theatre had retained another HVAC company to maintain the HVAC system and the maintenance contractor work coincided with the mold outbreak. After completion of discovery, dispositive motions were filed and the claims were dismissed against the insured.
Window Manufacturer
The insured is a large regional vinyl window manufacturer. While unloading windows at a new housing development, a hydraulic hose separated on the truck-mounted loading arm and releases hydraulic fluid onto a newly installed paved patio. Another subcontractor attempted to wash off the pavers and released contaminated water down a storm water drain. The local environmental regulators direct that the storm sewer be capped, flushed, and cleaned. The property developer submits a claim for the discolored paving stones and excavation of the soil beneath the pavers.
Pallet Manufacturer
The insured is a national pallet manufacturer, which has been operating at the site for over 30 years. During excavation for a new concrete pad for an outdoor storage area for pallet refurbishing, heavy oil staining and odor is found in the excavated soil. It is determined that the facility was used to manufacture rope and cable over 50 years ago and that waste oil was discarded in clay lined pits before being covered over with soil. The regulators direct remediation of the entire effected area. The rope and cable manufacturer only operated for a short period of time and was not listed on the phase 1 when the insured purchased the property.
Environmental Consultant
The insured is a national environmental consulting firm. The firm also performs system integrity testing for gas stations to confirm that the tanks and lines are secure. After a gas station undergoes renovation under new ownership, the insured is hired to test the USTs and lines and finds no issues. A few weeks later, the tanks are filled and a contractor is hired to connect the dispenser units and bring the system online. The contractor is unable to get the system to work, and an investigation commences. It is discovered that the lines from the tank to the dispenser units are severed and that significant quantities of gasoline have been released. The property owner alleges that the insured failed to or improperly conducted the tank tightness/line integrity test and therefore caused the release. The property owner demands that the insured pay for the remediation, including active ground water remediation. The employee who performed the testing has long since left the company and documentation is sparse.
Chemical Manufacturer
The insured is a leading chemical manufacturer. After a maintenance turnaround, the cracker units are brought back online. A loose flange causes gases to escape, which results in a flash fire and rupture of the feeder pipe, causing the release of gases. The plume spreads for several miles and almost 10,000 residents allege bodily injury. The claims are filed by several firms all seeking damages below the threshold required for a jury trial. The court rules that the plaintiffs do not have to show specific causation, and that they have met their burden by showing that the alleged injuries could have been caused by the release. The plaintiffs demand $50,000 each and the trial commences with 12 groups of plaintiffs.
Tank Cleaning Contractor
The insured is a local tank cleaning contractor hired by a multinational refiner to clean sludge from chemical tanks. During the cleaning, an insured employee opened an incorrect valve, causing a release of hydrogen sulfide gas. Eight employees of a contractor who was retained to perform routine maintenance at a refinery onsite were severely injured, and two died as a result of the exposure. Bodily injury claims are brought against the refinery and the insured. The refinery is an additional insured under the insured’s policy and tenders the defense.
Fertilizer Distributor
The insured is a large fertilizer distributor. Employees performing welding work on metal storage bin walls cause a bin of fertilizer to begin to smolder. Attempts by employees to douse the fire are unsuccessful and a full fire commences, spreading through the storage warehouse. The facility also stores ammonium nitrate. The local fire department responds, and upon learning of the ammonium nitrate stored onsite immediately, withdraws all firefighting personnel and equipment, creates a two-mile radius perimeter, and orders the evacuation of the town. Close to 50,000 people evacuate and numerous large processing plants shut down. The evacuation order is lifted eight hours later. Thousands of inconvenience, bodily injury, and property damage claims are brought. The fire burns out and there is no direct fire damage beyond the perimeter of the insured’s warehouse.
Gathering Line
The insured is a large regional oil and gas operator that has an extensive gathering line system. A dime sized hole occurred in a very remote wooded area of the a 4” mainline and was not discovered for months. When the landowner discovered the leak, the insured responded immediately and began repair and remediation operations. Within days of the remediation commencing the area was inundated with heavy rain and below freezing temperatures which was unprecedented for this region. This resulted in residue crude oil washing down stream into a small indigenous forest area. Due to the rain the area became inaccessible and a timber mats had to be trucked in to construct 2-mile access road to permit equipment access to the affected area as directed by the environmental regulatory agency. The rental and placement of the mats alone cost in excess of $1M. A creek in the forest had to be manually cleaned for over a month and various dykes and dams had to be constructed to catch contaminated rainwater to prevent further distribution of the residual crude oil that was not initially clean up. The clean-up project that prior to the inclement weather only impacted several hundred square feet took 90 days to complete and required the mobilization of significant equipment and personnel.
Produced Water Line Breach
The insured is a large independent operator that has operations in multiple states. A third- party trucker while exiting a remote site, after loading produced water at the site to transport to a disposal facility, ran over a produced water gathering line. The produced water released from the line for weeks and due to the soil type migrated into the soil and ran down gradient to an adjacent landowner field impacting several acres of arable soil and crops. Almost 3’ of soil had to be excavated and transported to a disposal facility over 60 miles away and new soil had to be trucked in. The project was completed in 60 days. The third-party trucker did not carry appropriate insurance and the trucker sought bankruptcy protection.
Methane Water Well Contamination
The insured is a large national oil and gas operator, with operations in 5 states. The insured acquired assets from another operator and shortly after completion of the acquisition, an adjacent landowner notified the insured of well water anomalies (air locks in their boiler and bubbling in the well). Baseline well water sampling had been performed on a nearby water well prior to the construction of the oil well, some 4 years before acquisition. Water sampling was completed which indicated methane levels that required reporting to the regulators. The regulatory agency directed that all water wells within a ¾ mile radius of the insured wells and other operator wells be tested and isoptope matching be completed. The isotope matching indicated that the methane was thermogenic, and since all operator wells involved the same pay zone, it was virtually impossible to identify the exact source. Each operator had had some gas pressure anomalies at the bradenhead of various wells post construction, which the prior operator had dealt with. Over 10 water wells revealed elevated methane levels and some thermogenic isotopes. Methane mitigation systems were installed on each of the water wells, and drinking water was trucked in. Several landowners subsequently filed suit for bodily injury and property damage (diminution in property value).
SWD Release
The insured is a small independent regional operator that owns and operates several saltwater disposal facilities (SWD’s). One the SWD’s has a casing failure and leaks, contaminating area groundwater for months before the issue is discovered. Several stock water and irrigation wells were contaminated. Remediation systems are put in place for long term remediation of the contamination, and temporary water supplies are provided during the multi-year remediation. The aquifer is at depth which significantly increased the cost of the remediation system.
Air Pollution
The insured is a national operator with operations in virtually every shale play. A local group of adjacent landowners in one state, supported by a large national environmental group, files suit alleging bodily injury, nuisance and trespass as a result of exposure to the various fugitive emissions from oil and gas operations (including compressor stations). The environmental group wanted to make an anti- hydrocarbon statement and attempted to leverage this litigation as starting point for nationwide toxic tort litigation.
Flooding
The insured is a small regional operator. During a significant rain event and subsequent flooding numerous well pads are inundated with flood water. While the operator was proactive in shutting in all the wells, numerous tanks are overturned spilling the contents and contaminating surrounding areas. In addition, numerous retention ponds were overwhelmed and overtop releasing contaminated water onto adjacent crop lands ruining the crop and contaminating the soil. The clean-up was severally hampered by infrastructure damage limiting access and discovery of the contamination. Lack of availability of local contractors to complete the clean-up. Out of state contractors were brought in to mitigate and complete the remediation.
Benzyne
The plaintiff is an independent engineer that over his working life performed various engineering services for numerous oil and gas operators. He is diagnosed with a rare cancer and bring suit against virtually all the operators he worked for alleging that his exposure to benzene during this work caused his cancer and acute toxicity to his nervous system, liver and kidneys. While numerous operators settled out, the remaining operators took the matter to trial and refused to settle within their respective self-insured retentions. A significant adverse verdict was rendered, and numerous similar copycat suits were filed.
Impoundment Release
The insured is a small regional operator that has several synthetically lined impoundments. One of the impoundments sustained a breach in the liner (cause unknown) and released significant volumes of produced water. The contamination migrated offsite onto adjacent crop land and down to an aquifer used by a nearby town. 5 acres of farmland was remediated by in situ soil remediation and alternate water sources were required for the town water supply for several years while the aquifer remediation was completed. Several homeowners in the town filed suit alleging bodily injury and property damage (diminution of value).
Storage Yard Contamination
The insured is a large oil and gas operator that has large equipment yards throughout the oil production area. During an expansion project at two yards, soil samples revealed elevated levels of chemicals used in oil and gas drilling and production. The regulatory agency was notified and directed that the yards be cleaned up and further directed that the remaining yards be tested for similar chemical constituents. Several adjacent property owners brought suit alleging offsite migration of the chemicals contaminated their properties.
Salt-Water Disposal Facility Permit Violations
A large saltwater disposal facility is sued by the local regulators for violating their disposal permits and improperly injecting oilfield waste materials. The SWD operator alleges that oil and gas operators and their truckers were improperly characterizing the waste and should bresponsible for any contamination and the clean-up thereof. All manifests were scrutinized and all operators that disposed of waste to this facility were sued by the regulators and adjacent landowners who claimed that the water aquifer had been contaminated by the waste disposal.
Legacy Operations
Numerous landowners that had historical oil and gas well leases on their properties, brought suit against the operators and interest owners alleging that during the legacy operations decades ago the operators contaminated the soil and water on their properties. Property owners sought clean-up expenses, property damage and bodily injury, including fear of cancer.